Our Silicone Transfer Molding
Silicone transfer molding is an advanced manufacturing technique that effectively integrates elements of both injection and compression molding. This method simplifies the complexities associated with injection molding by utilizing a more straightforward setup. In transfer molding, silicone material is initially loaded into a transfer pot before being directed into the mold cavity. This process marries the precision of injection molding with the less complex equipment typically used in compression molding. As a result, silicone transfer molding is particularly adept at producing medium-volume runs of high-quality parts with intricate designs and precise tolerances, making it ideal for applications involving silicone materials.
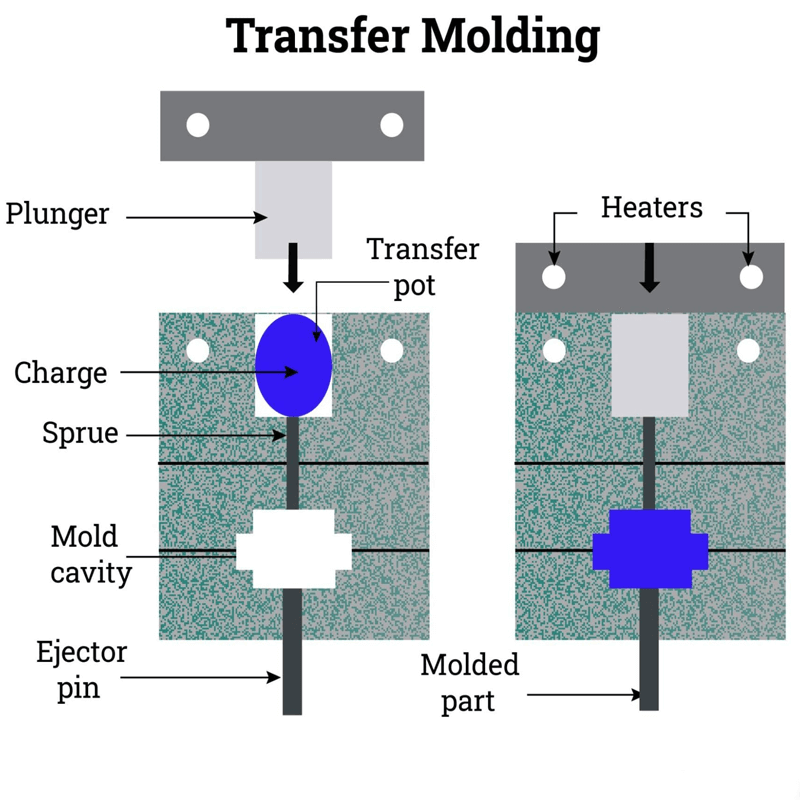
Silicone Transfer Molding Process
1. Material Preparation
The silicone rubber, consisting of a base and a curing agent, is precisely mixed in a specified ratio to achieve consistent chemical properties throughout the batch.
2. Loading the Material
The blended silicone compound is carefully loaded into a transfer pot positioned above the mold cavity. This step ensures that the correct amount of silicone is prepared for transfer into the mold, optimizing control over the material's movement and application.
3. Molding Press Closure
The mold, which consists of multiple metal halves, is closed around the transfer pot. This configuration forms a sealed environment essential for managing the heat and pressure required during the transfer and curing processes, defining the final part's shape, texture, and intricate details.
4. Material Transfer
Upon closing the mold, heat and pressure are applied, causing the silicone to flow through a gate into the mold cavity. The heat reduces the viscosity of the silicone, enabling it to fill the mold cavities completely, while the pressure ensures the accurate replication of detailed features.
5. Curing
Once the mold cavity is filled, the silicone undergoes a curing process where the material transitions from a liquid to a solid state. The heat activates the curing agent within the silicone compound, initiating cross-linking within the silicone polymer. This curing process imparts the final part with its desired structural strength and physical properties.
6. Mold Opening and Part Ejection
After curing, the mold is opened, and the finished silicone part is ejected. The mold design, often featuring draft angles and ejector pins, facilitates the easy removal of the cured part, ensuring that it adheres to the mold's design specifications.
7. Post-Processing
The completed part may require trimming to eliminate any excess material (flash) and might undergo further finishing processes or quality inspections. This post-processing phase ensures that the final product adheres to all dimensional and aesthetic quality standards.
Why Choose Milosilicone for Your Silicone Transfer Molding
1. Expertise in Silicone Materials
At Milosilicone, we bring extensive experience and expertise in working with a diverse range of silicone materials, including High Consistency Rubber (HCR), Liquid Silicone Rubber (LSR), and Fluorosilicone Rubber (FSR). Our deep understanding of these materials ensures that we can meet your specific requirements for precision, durability, and performance.
2. Advanced Transfer Molding Technology
Our state-of-the-art transfer molding equipment is designed to optimize both efficiency and accuracy. We utilize advanced technology to reduce cycle times and enhance part consistency, delivering high-quality silicone products with intricate details and tight tolerances.
3. Commitment to Quality
Milosilicone adheres to stringent quality control processes to guarantee that each silicone part meets the highest standards. Our rigorous testing and inspection procedures ensure that every product we manufacture is reliable, durable, and conforms to your specifications.
4. Customization and Flexibility
We offer tailored solutions to address your unique design and production needs. Whether you require high-volume production or specialized silicone parts, our flexible approach and comprehensive capabilities allow us to adapt to various project requirements, ensuring optimal results for your silicone transfer molding needs.
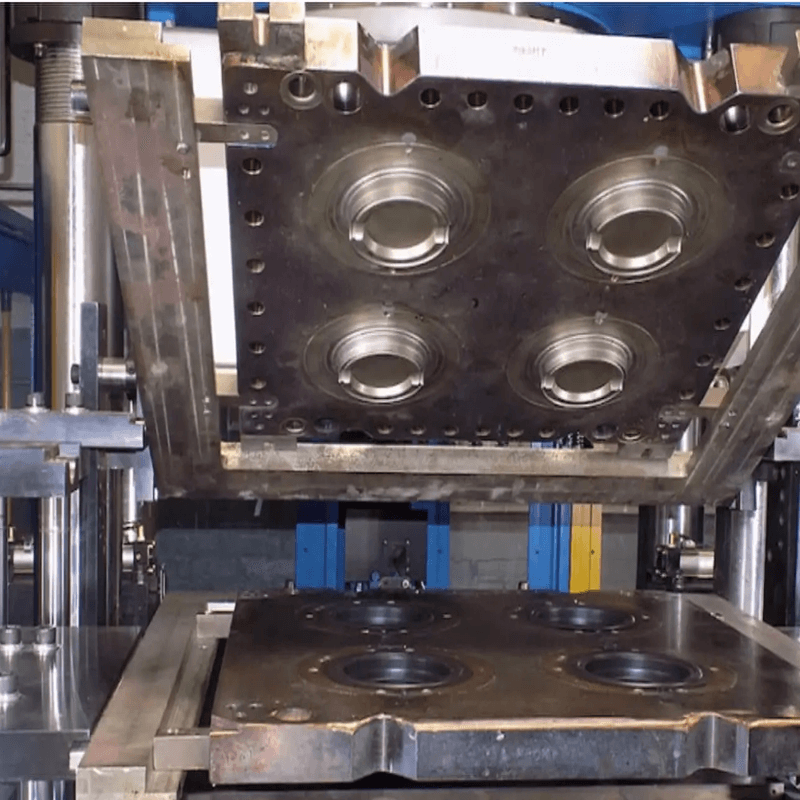
The Advantages of Silicone Transfer Molding
1. High Precision and Detail
Silicone transfer molding excels in producing parts with intricate details and tight tolerances. The process ensures accurate replication of complex designs, making it ideal for applications requiring high precision.
2. Versatile Material Compatibility
This molding technique is compatible with a variety of silicone compounds, including both standard and custom formulations. This versatility allows for the production of parts with specific material properties tailored to different applications.
3. Efficient Production for Medium Volumes
Silicone transfer molding strikes a balance between the high-volume efficiency of injection molding and the simplicity of compression molding. It is particularly effective for medium-volume production runs, providing a cost-effective solution without sacrificing quality.
4. Enhanced Surface Finish
The process often results in superior surface finishes compared to other molding techniques. The controlled environment of transfer molding minimizes defects such as air bubbles and surface imperfections, leading to a smoother final product.
5. Reduced Waste and Improved Yield
The transfer molding process minimizes material waste by precisely controlling the amount of silicone used. This efficiency not only reduces costs but also contributes to a more sustainable manufacturing process.
6. Lower Tooling Costs
Compared to injection molding, the tooling for silicone transfer molding is generally less complex and less expensive. This makes it a cost-effective option for producing high-quality silicone products, especially for applications with moderate production volumes.
Silicone Materials for Transfer Molding
Silicone transfer molding is highly adaptable, utilizing various silicone materials to meet diverse application requirements. Here’s an overview of the key silicone materials used in this process:
High Consistency Rubber (HCR) / High-Temperature Vulcanizing (HTV) Silicones
High Consistency Rubber (HCR), also known as High-Temperature Vulcanizing (HTV) silicone, is a preferred material in transfer molding due to its high viscosity and the need for heat to initiate curing. HCR is pre-mixed with curing agents and any necessary additives before being loaded into the transfer pot. During the molding process, heat and pressure facilitate the flow of HCR into the mold cavity, where it cures to form the final product, making it suitable for producing durable parts with precise dimensions.
Liquid Silicone Rubber (LSR)
While Liquid Silicone Rubber (LSR) is commonly associated with injection molding, its low viscosity makes it applicable for transfer molding as well. LSR's excellent flexibility, thermal stability, and chemical resistance are ideal for manufacturing intricate parts that require high precision, such as those used in medical devices. The transfer molding process enables LSR to be easily shaped into complex geometries and fine details, ensuring high-quality performance and hygienic standards.
Fluorosilicone Rubber (FSR)
Fluorosilicone Rubber (FSR) is known for its superior resistance to chemicals, fuels, and oils, making it particularly valuable for demanding automotive and aerospace applications. Transfer molding is effective for producing seals and gaskets from FSR, as it allows for the creation of parts that maintain their integrity and performance under harsh chemical conditions.
Choosing the appropriate silicone material for transfer molding is crucial and depends on the specific requirements of the final application, ensuring optimal performance and durability of the silicone products.
Differences Between Silicone Transfer Molding and Other Molding Methods
Compression Molding vs. Silicone Transfer Molding
Silicone transfer molding offers notable advantages over compression molding in terms of cycle time efficiency. Compression molding typically requires 2-3 minutes per cycle, whereas silicone transfer molding completes a cycle in approximately 30-45 seconds. This significant reduction in cycle time is attributed to the streamlined press and pre-form design of silicone transfer molding, which enhances overall productivity and efficiency.
Injection Molding vs. Silicone Transfer Molding
Although silicone transfer molding and injection molding share similarities, they differ in several key aspects. Injection molding operates at much higher pressures, ranging from 10,000 to 30,000 PSI, whereas silicone transfer molding functions at lower pressures, typically between 1,500 and 2,500 PSI. This lower pressure in silicone transfer molding results in reduced wear and tear on the equipment. Additionally, silicone transfer molding is preferable for processing materials that are sensitive to high pressures, as it maintains better part integrity and reduces the risk of defects.