What Is Silicone Compression Molding
Silicone compression molding, also known as rubber compression molding or compression mold tooling, is a widely utilized technique for producing a variety of elastomeric silicone rubber parts and products. This process is versatile and can accommodate both simple designs, such as O-rings and washers, as well as more complex precision components.
Silicone compression molding involves the use of specialized molds and equipment to shape silicone products. The quality and precision of the molded parts are influenced by several factors:
- Mold Plate Steel: The choice of high-grade mold plate steel ensures durability and accuracy in part production.
- Mold Components: Precision-engineered mold parts contribute to the overall quality and consistency of the molded silicone products.
- Mold-Making Equipment: Advanced mold-making technology is essential for achieving high-quality results.
- Process Controls: Effective management of the compression molding process is crucial for maintaining precise dimensions and performance.
This molding technique allows for the production of both simple and intricate silicone parts, making it a preferred choice for applications across various industries. For high-quality silicone products tailored to your specific needs, silicone compression molding offers reliable and efficient solutions.
Silicone Compression Molding Process
1. Preheating the Mold:
- The silicone mold is preheated to the required temperature, typically between 160°C and 200°C, to prepare it for the molding process.
2. Loading the Raw Material:
- Specific silicone raw materials are placed into the mold cavities. These materials are carefully measured to ensure consistency and quality in the final product.
3. Mold Closure and Compression:
- The mold is closed, and a compression machine applies pressure to the mold. This pressure forces the silicone material to flow evenly into all cavities.
4. Heating and Curing:
- With the application of heat and pressure, the silicone material cures and solidifies. The temperature and pressure settings are crucial to achieving the desired properties of the silicone product. Too low a temperature may lead to incomplete curing, while too high a temperature can cause cracking.
5. Curing Time:
- The curing time depends on the design, weight, and thickness of the silicone rubber seal. It is essential to monitor and adjust the curing time to ensure optimal results.
6. Final Inspection:
- After curing, the silicone products are removed from the mold and inspected for quality and consistency. This final step ensures that the products meet the required specifications and performance standards.
Types of Silicone Compression Molds
Silicone compression molding is a cost-effective method for producing silicone rubber seals and other parts. The various types of silicone compression molds are designed to accommodate different complexities in part design and manufacturing needs. Here is a breakdown of the primary mold types:
1. Two-Plate Silicone Compression Mold:
- This is the most basic and commonly used mold, consisting of two tool plates. The cavities for silicone products are machined into these two plates. This mold type is ideal for simple silicone components, such as O-rings and flat rubber gaskets. It offers a straightforward approach to producing basic silicone parts efficiently.
2. Two-Plate Mold with a Middle Plate:
- This mold configuration is suitable for silicone products that feature small undercuts, such as rubber grommets. The middle plate allows for the production of parts with slight geometric complexities. After curing, the middle plate must be removed to extract the silicone part. For grommets with small undercuts and a softer durometer (approximately 30 Shore A - 60 Shore A), this type of mold is effective. However, for grommets with larger undercuts or higher hardness (above 80 Shore A), the middle plate approach may be impractical due to difficulties in demolding. In such cases, molds with cores are recommended.
3. Silicone Rubber Compression Mold with Mold Cores:
- Molds with cores are designed for silicone products that have deep undercuts or cylindrical shapes, such as grommets and silicone bottle sleeves. The cores create the necessary features in the silicone part, and the final product is demolded from the cores. This mold type is suitable for producing more intricate silicone parts with parting lines on both sides.
4. Silicone Rubber Compression Mold with Sliders:
- For complex silicone parts with deep undercuts or hollow cylindrical shapes, molds with sliders are used. Sliders allow for the creation of these intricate features but may extend the production cycle time due to the additional steps required for demolding. Furthermore, molds with sliders typically have a shorter mechanical lifespan and may exhibit more visible parting lines as the mold is used over time.
Each type of silicone compression mold is designed to meet specific manufacturing needs and complexities, ensuring that silicone products can be produced with high precision and efficiency.
Precision Rubber Seals Compression Molds
Milosilicone has been specializing in the production of precision rubber seals through compression molding for over six years. Our expertise encompasses the manufacturing of high-precision seals including nitrile seals, neoprene gaskets, silicone O-ring gaskets, and EPDM rubber washers.
In our compression molding process, we achieve a remarkably low flash tolerance, with some molds producing flash as minimal as 0.03 mm, and most consistently below 0.07 mm. This precision ensures that our silicone products meet stringent quality standards.
For liquid silicone injection molding, we offer silicone rubber gaskets that are completely flash-free. Our advanced molding techniques ensure that every silicone part maintains consistent wall thickness and exhibits high-quality performance and durability.
We are committed to delivering silicone products with exceptional precision, consistency, and reliability, making us a trusted partner for high-quality rubber seals and gaskets.
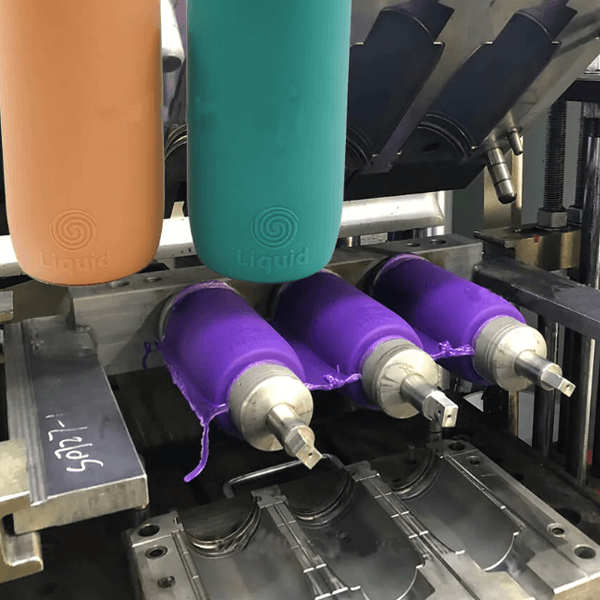
The Application Industries of Silicone Compression Molding
1. Automotive Industry
Silicone compression molding is widely utilized in the automotive sector for producing durable, high-performance silicone products such as seals, gaskets, and vibration dampers. These silicone components are essential for ensuring reliable performance in demanding environments under the hood, including resistance to extreme temperatures and harsh chemicals.
2. Medical and Healthcare Industry
In the medical field, silicone compression molding plays a crucial role in manufacturing biocompatible and sterilizable silicone products. Common applications include medical seals, gaskets, and components for devices like respiratory equipment, surgical tools, and patient care products, all of which must meet stringent health and safety standards.
3. Consumer Goods
The consumer goods sector benefits from silicone compression molding for producing a wide range of silicone products. These include kitchenware, household items, and personal care products that require durability, flexibility, and resistance to heat and chemicals, such as silicone baking mats, seals, and waterproofing components.
4. Industrial Applications
Silicone compression molding is essential in various industrial applications for manufacturing robust silicone products like seals, gaskets, and protective components. These silicone parts are designed to withstand high temperatures, pressure, and aggressive chemicals, making them ideal for use in machinery, equipment, and industrial systems.
These industries leverage the advantages of silicone compression molding to achieve high-quality, reliable silicone products tailored to their specific needs.