Our Plastic Injection Molding
Plastic injection molding is a highly efficient manufacturing process used to produce a wide variety of plastic parts and components. This process involves injecting molten plastic material into a precisely engineered mold cavity, where it cools and solidifies into the desired shape.
The plastic injection molding process begins with the heating of thermoplastic or thermosetting polymers until they reach a molten state. The molten plastic is then injected into a mold under high pressure using a specialized injection molding machine. Once the material fills the mold cavity, it is held under pressure until it cools and solidifies. After solidification, the mold opens, and the finished part is ejected.
This method is known for its ability to produce complex, intricate designs with high precision and repeatability, making it ideal for mass production. It is widely used across various industries, including automotive, electronics, medical devices, consumer goods, and packaging, where consistent quality and cost-effectiveness are paramount.
Plastic injection molding offers several key advantages, including the ability to produce large volumes of parts quickly and with minimal waste. Additionally, the process supports a wide range of materials, allowing manufacturers to select plastics with specific properties to meet the functional requirements of the final product. The versatility, efficiency, and scalability of plastic injection molding make it a cornerstone of modern manufacturing.
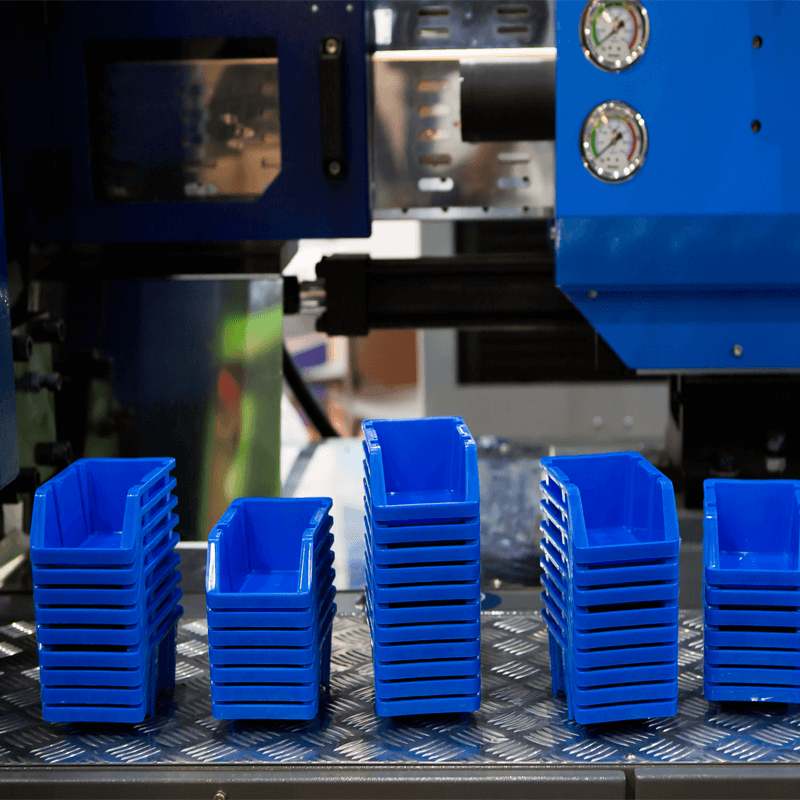
The Plastic Injection Molding Process
Plastic injection molding is a precise and efficient method for producing parts by injecting molten plastic resin into a mold under high pressure. The mold can range from a single cavity to multiple cavities, allowing for the mass production of parts. Once the mold design and manufacturing are complete, the injection molding process follows these fundamental steps:
Step 1: The process begins with raw plastic resin in the form of pellets. These pellets are first dried to achieve the correct moisture content. If required, the pellets are then mixed with pigments or masterbatch colorants to achieve the desired color for the final product.
Step 2: The dried and, if necessary, colored pellets are fed into the hopper of the injection molding machine. Inside the machine's barrel, a reciprocating screw transports the pellets towards the mold, while simultaneously heating them.
Step 3: As the pellets move through the barrel, they are thoroughly mixed and heated until they reach a molten state, transforming into liquid resin.
Step 4: The heated mold automatically closes, and the molten resin is injected under high pressure through a gate system into the mold cavity.
Step 5: The mold is then rapidly cooled, allowing the molten resin to solidify and take the shape of the cavity.
Step 6: Finally, the mold opens, and the solidified part is ejected, ready for the next production cycle to begin.
This systematic process enables the production of high-quality, consistent parts suitable for a wide range of applications across various industries.
Benefits of Plastic Injection Molding
Plastic injection molding offers numerous advantages, making it a preferred manufacturing method for high-volume production. Key benefits include the capability to produce large quantities of parts rapidly, superior surface finishes, extensive material options, color versatility, and long-lasting tooling.
- Vast Selection of Resins: A wide variety of resins are available, providing flexibility in material choice to meet specific performance and aesthetic requirements.
- Economies of Scale: This process is highly cost-effective for large production runs, reducing the cost per unit as production volumes increase.
- Consistency and Repeatability: Plastic injection molding ensures stable and repeatable production, delivering parts with consistent quality and precision.
- Superior Surface Finish: The process achieves high-quality surface finishes, reducing the need for additional post-processing.
- Overmolding Capabilities: Overmolding allows for complex designs by combining multiple materials, enhancing product functionality and aesthetics.
- Multi-Cavity and Family Tooling: The use of multi-cavity and family molds enables the efficient production of multiple parts in a single cycle, further optimizing manufacturing efficiency.
Why Choose Milosilicone for Plastic Injection Molding
At Milosilicone, we believe that the best production molds begin with high-quality raw materials, stringent process controls, and the expertise of skilled toolmakers. Here’s why Milosilicone is the ideal choice for high-volume production tooling and plastic injection molding services:
Comprehensive Services
Milosilicone goes beyond just toolmaking and molding. We provide a full suite of manufacturing processes, offering a complete product development solution tailored to your needs.
Proven Track Record
We’ve earned the trust of thousands of companies worldwide, from startups to industry leaders, helping them create innovative injection molds and finished parts. Your success is the cornerstone of our reputation.
Material Verification
Our advanced material verification processes ensure full compliance with industry regulations, providing you with confidence and peace of mind. When precision matters, businesses turn to Milosilicone to get the job done right.
Design Enhancement
Each project benefits from our thorough design-for-manufacturing (DFM) review. This ensures that you receive optimized designs that deliver outstanding results while minimizing time and costs.
Injection Molding Tolerances
Plastic resins naturally expand and contract due to factors like temperature fluctuations, mechanical stress, and moisture absorption. To assist in your design process, our tolerance guide offers insights into the shrinkage behaviors of commonly used resins.
During our design analysis, we meticulously identify any potential areas that could lead to thermal stress, shrinkage, warping, or other preventable defects in your injection-molded components. For further details, refer to our comprehensive manufacturing design guide, which covers common defects and strategies to prevent them.
In the absence of specific requirements, we adhere to the DIN 16742 standard tolerances for injection molding, ensuring that the highest quality standards are met throughout our production process. Additionally, our visual quality standards guide is applied rigorously to all injection-molded parts to maintain superior quality.
Applications of Plastic Injection Molding
Medical Industry
Plastic plays a pivotal role in the medical industry due to its lightweight, non-toxic, cost-effective, and versatile nature. Medical devices such as syringes, catheters, dispensers, tubing, and various other instruments are commonly made using plastic injection molding. For a deeper dive into how this process is utilized in healthcare, explore our detailed blog post on the subject.
Consumer Products
Plastic is an integral part of everyday life, used in countless consumer products. From computer peripherals like keyboards and mice to gaming controllers, headphones, toys, home appliances, and kitchen tools, plastic compounds with diverse chemical properties are ubiquitous. Discover more about the role of plastic in consumer goods and its wide-ranging applications.
Electronics Industry
In electronics, plastic injection molding is essential for creating robust, lightweight, and non-conductive enclosures that protect sensitive components such as circuit boards, switches, wiring, batteries, and sensors. These housings not only shield the components but also ensure user safety. Learn why plastic injection molding is the go-to solution for electronics manufacturing.
Agriculture Industry
Agricultural applications demand plastic products that are strong, durable, and resistant to UV exposure and chemicals. Engineered plastic parts are utilized in various farming equipment, including conveyor belts, drive systems, feeders, water sprinklers, fencing, and tools. Explore the advantages of plastic injection molding in meeting the rigorous demands of the agriculture industry.