Our LSR Injection Molding
Liquid Silicone Rubber (LSR) molding is a sophisticated process designed to produce durable, flexible, and high-precision parts in large quantities. This method is renowned for creating components that are highly water-resistant and resilient, making them ideal for applications such as seals, membranes, electrical connectors, and various medical, commercial, and consumer products.
Also known as Liquid Injection Molding (LIM), this technique involves injecting liquid silicone into pre-designed molds. The silicone is then allowed to cure within the mold, creating parts that meet stringent quality and precision standards. The process is repeated until the desired production volume is achieved, ensuring consistent and reliable results across a wide range of silicone products.
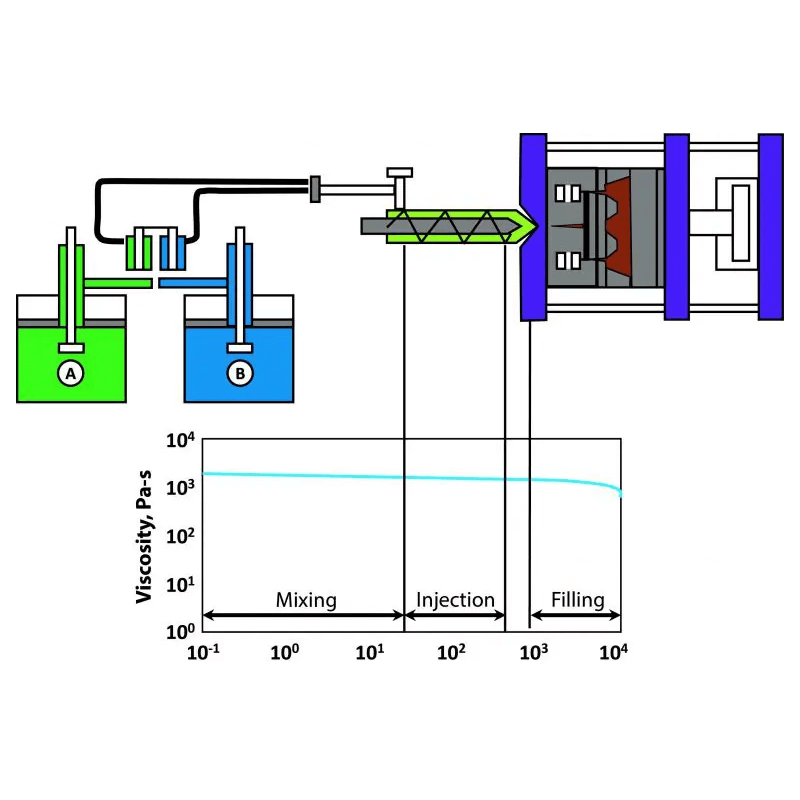
Characteristics Of Liquid Silicone Rubber (LSR)
Biocompatibility: Liquid Silicone Rubber (LSR) exhibits exceptional biocompatibility, demonstrating superior compatibility with human tissue and body fluids through rigorous testing. Unlike other elastomers, LSR resists bacterial growth and does not stain or corrode other materials. It is both tasteless and odorless and can be formulated to meet stringent FDA regulations. LSR can be effectively sterilized using various methods, including steam autoclaving, ethylene oxide (ETO), gamma radiation, e-beam, and others.
Durability: LSR components are highly durable, capable of withstanding extreme temperatures, making them suitable for automotive applications and environments near engines. Parts produced via LSR injection molding are fire-resistant and will not melt, addressing a common issue seen with components manufactured through plastic injection molding.
Chemical Resistance: LSR offers excellent resistance to water, oxidation, and various chemical solutions, including acids and alkalis. This makes it highly suitable for applications exposed to harsh chemical environments.
Temperature Resistance: Molded LSR maintains stability across a broad temperature range, outperforming many other elastomers. For instance, Silastic LSR by Dow Corning remains stable at temperatures from –60°C to +180°C, making it ideal for applications with extreme temperature variations.
LSR Molded Part Design and Materials
Liquid Silicone Rubber (LSR) parts possess unique inherent properties, including high elasticity, strength, and excellent thermal, chemical, and electrical resistance. These components retain their physical characteristics even under extreme temperatures and are capable of withstanding various sterilization methods. LSR’s biocompatibility makes it particularly suitable for applications involving skin contact. These attributes are highly valued in automotive, medical, and food appliance industries, where LSR is commonly used for seals, gaskets, valves, and cables.
Designing parts for LSR requires attention to specific guidelines, although it shares similarities with thermoplastic design. Key considerations for LSR part design include:
- Material Specifications, Grades, and Durometer: Select the appropriate grade and durometer of LSR to match the part’s requirements.
- Part Size: Ensure that the design accommodates the part's dimensions within the molding constraints.
- Shot Size: Optimize the amount of material injected to achieve desired results.
- Dimensional Accuracy: Maintain tight tolerances to ensure precision and functionality.
- Shrinkage: Account for material shrinkage during cooling to ensure proper fit and function.
- Drafts and Undercuts: Incorporate draft angles and avoid undercuts to facilitate mold release.
- Parting Lines/Split Lines: Design parting lines to minimize their impact on the part’s functionality and appearance.
- Gates: Position gates strategically for optimal material flow and minimal waste.
- Aesthetics: Consider surface finishes and appearances in the design process.
The most commonly used material in the LSR molding process is high-purity platinum-cured silicone, known for its durability and suitability across various industries. In the medical field, LSR is favored for its biocompatibility and ability to reduce contamination risks in tools and instruments. Fluoro liquid silicone rubber is another material making significant strides, especially in automotive applications and for parts requiring extreme precision.
Liquid Silicone Rubber Injection Molding Process
For over 20 years, Milosilicone has been delivering high-quality liquid silicone rubber (LSR) injection molding services to brands, wholesalers, and retailers, specializing in both medical and consumer goods. Our state-of-the-art facility is equipped with six advanced LSR molding machines, allowing us to produce a diverse range of silicone products, with a focus on customized solutions for both consumer and medical applications. As a comprehensive silicone products manufacturing facility, we are committed to meeting your scalability needs with precision and efficiency.
The Liquid Silicone Rubber Injection Molding Process:
1. Material Preparation:
- The process begins with two components, Compound A and Compound B, stored in separate containers. Compound A contains the base material, while Compound B holds the catalyst. These components are fed into a pumping system that ensures a precise one-to-one mixing ratio.
2. Injection Molding Setup:
- The automated injection-molding machine is programmed to deliver the correct shot size for each production run. Key parameters such as temperature, pressure, injection rate, and cycle time are meticulously adjusted to align with specific customer requirements. The machine’s platens and pistons are set to control mold alignment and clamping force.
3. Mold Heating and Injection:
- The mold is heated to the designated temperature, and clamping force is applied. The mold closes in sync with the machine's injector and pump system. The liquid silicone is then injected into the mold cavities under controlled conditions.
4. Curing and Part Removal:
- The combination of heat and pressure causes the liquid silicone rubber to cure and solidify within the mold. Once the curing cycle is complete, the mold opens, and the silicone parts, along with any flashing, are removed. This can be done either automatically or manually, depending on the setup.
5. Post-Molding Processes:
- After removal, the parts undergo post-molding operations, which may include de-flashing, post-curing, inspection, and packaging to ensure they meet quality standards.
Milosilicone’s expertise in LSR injection molding and our commitment to delivering high-quality silicone products ensure that we can meet your specific needs and maintain the highest standards in production.
Custom Molded LSR Solutions for Your Business
At Milosilicone, we specialize in delivering tailored solutions for molded silicone rubber components, aligning with your specific timelines and budgets. Our exclusive focus on silicone products ensures mastery in both high-quality Liquid Silicone Rubber (LSR) and LSR 2-Shot molding processes. We elevate the concept of "custom" by offering comprehensive LSR molding solutions designed to meet the precise needs of your business.
As a leading manufacturer of Liquid Silicone Rubber parts, we serve some of the world’s largest enterprises across automotive, medical, life sciences, industrial, and consumer markets. Our expertise spans every aspect of design and production, including:
- Material Selection: Assistance in choosing the optimal grade of LSR to suit your application.
- Design Support: Expertise in design for manufacturability (DFM) to enhance part performance and ease of production.
- Tooling: Provision of high-quality tooling for precise and reliable molding.
- Production and Packaging: Efficient high-volume production and packaging solutions to minimize overhead costs.
Our custom-designed LSR products and LSR 2-Shot parts are crafted to meet the highest standards of quality. We offer cost-effective prototypes and small production runs that fit your schedule and project requirements.
For high-quality, custom silicone rubber products, contact us today to request a quote and discuss how we can support your business needs.
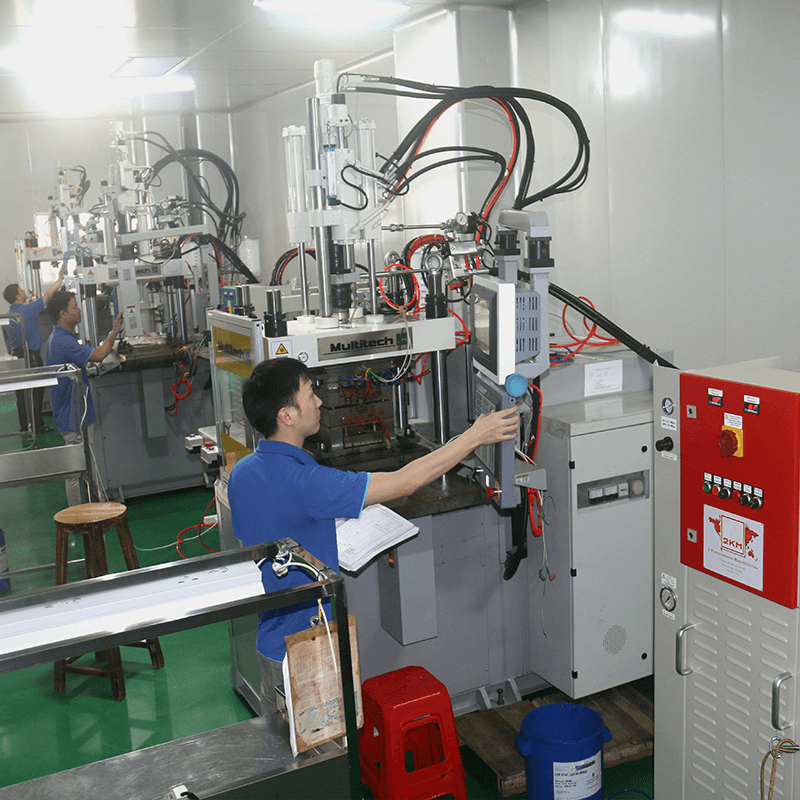
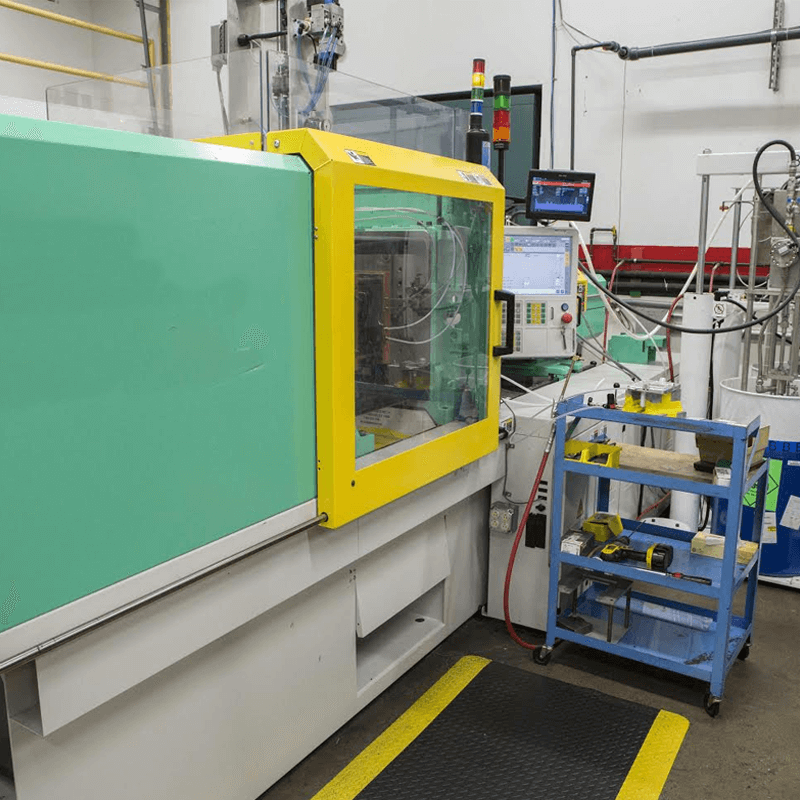
Our LSR Quality Standards
Ensuring top-tier quality in liquid silicone rubber (LSR) molding demands a rigorous approach throughout every stage of production, from product design and tooling to prototyping and final assembly. A silicone rubber molding manufacturer must possess the expertise and commitment to meet the highest standards of precision and reliability. Key elements of an effective quality assurance program for LSR injection molding include:
1. Stringent In-Process Inspection:
- Continuous monitoring of LSR parts during production is essential to detect and address any defects, damage, or inconsistencies in real-time. This ensures that every silicone product meets stringent quality requirements before moving forward.
2. Comprehensive Quality Programs:
- Implementing robust quality programs is crucial to achieving first-pass success in production, thereby saving time, reducing costs, and preserving your brand’s reputation. Effective quality control measures are designed to prevent errors and ensure that silicone products are manufactured to exacting standards.
3. ISO Certification:
- As an ISO 9001:2015 and ISO 14001:2015 certified company, we adhere to internationally recognized quality and environmental management standards. Our extensive experience, with over 1,000 projects completed for leading brands in the baby care, medical, and other global industries, underscores our proven ability to deliver high-precision silicone products of exceptional quality.
At Milosilicone, our dedication to maintaining rigorous quality standards ensures that every silicone product we manufacture meets the highest benchmarks of performance and reliability.