About Us
Milosilicone is a leading manufacturer specializing in the research, development, design, and production of high-quality silicone products.
Our company boasts an in-house design team, a dedicated molding department, state-of-the-art production lines, as well as specialized departments for printing, assembly, inspection, packaging, and logistics. We are proud to hold certifications including BSCI, FDA, LFGB, ROHS, and REACH, with our factory also being BSCI and ISO9001 certified.
We use only food-grade silicone that complies with FDA and LFGB standards. Our product range includes silicone kitchenware, silicone baby and maternity products, silicone consumer goods and pet toys, silicone electronic accessories, and various plastic and rubber products. The primary materials we work with include silicone, PP, and stainless steel components.
Our silicone products are primarily exported to Europe, North America, Japan, Oceania, and the Middle East. Since our establishment, we have earned a strong reputation among customers for our commitment to quality, competitive pricing, and advanced manufacturing techniques. We warmly welcome OEM service inquiries and look forward to collaborating with you.
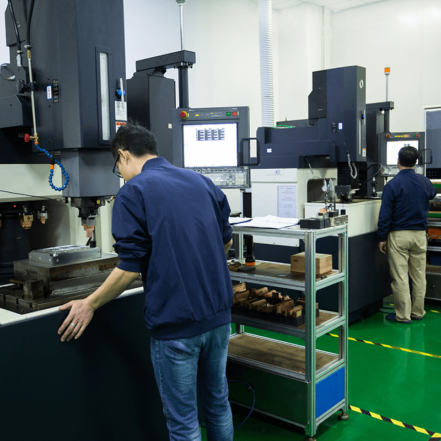
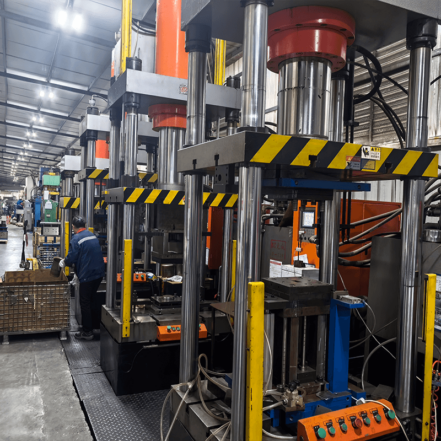
Why Choose Us?
Professional Team
Put your concerns at ease by working with our dedicated, professional team at Milosilicone. With over a decade of experience in the silicone industry, our engineers, designers, and account representatives are well-equipped to provide you with exceptional service and expertise in silicone products.
Customized Silicone Solutions Tailored to Your Needs
At Milosilicone, we prioritize the specific needs of each customer. We meticulously manage every aspect of your project, crafting bespoke silicone solutions that ensure optimal results and exceed your expectations.
Uncompromising Quality Assurance
Quality is the cornerstone of everything we do at Milosilicone. Our factory proudly holds ISO, SEDEX, and BSCI certifications, reflecting our commitment to the highest manufacturing standards. Additionally, our silicone products are certified by FDA, CE, LFGB, and CPC, guaranteeing that the silicone products you receive are not only safe and reliable but also of the highest quality.
State-of-the-Art Manufacturing Equipment
At Milosilicone, we utilize advanced production equipment to deliver superior quality silicone products. Our capabilities include silicone compression molding, silicone injection molding, and plastic injection molding. This cutting-edge technology allows us to efficiently produce high-precision parts with exceptional consistency, ensuring that every product meets the rigorous standards our clients expect.
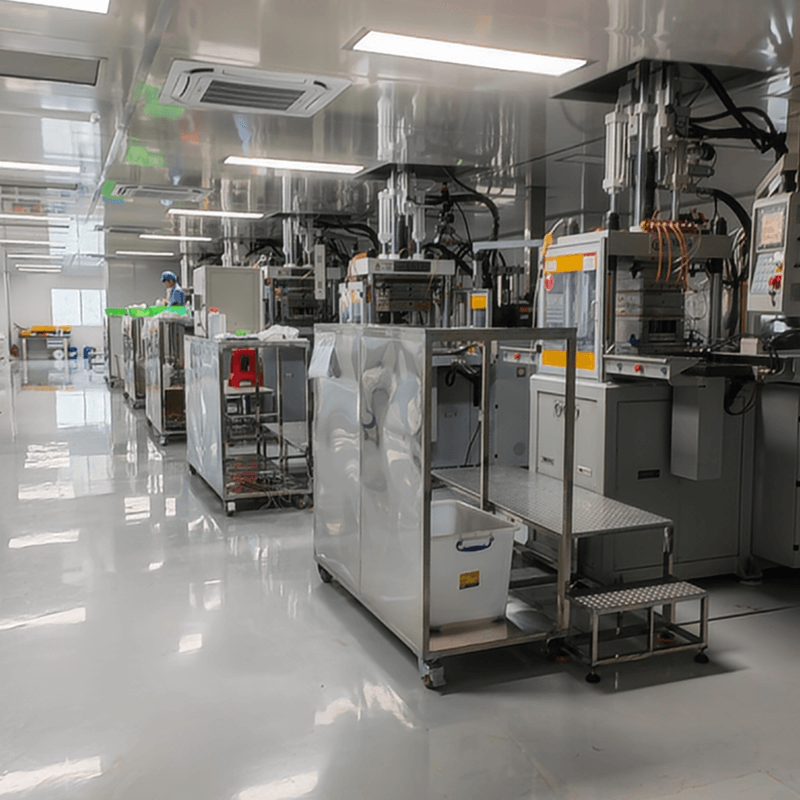
Our Factory
We operate an in-house tool shop to maintain complete control, confidentiality, and flexibility throughout the production process. Our advanced machinery infrastructure supports eco-friendly and high-quality manufacturing of silicone products using precision tools. By managing the entire production chain internally, we ensure optimal process safety and cost efficiency.
Our comprehensive suite of manufacturing technologies encompasses mold design and fabrication, silicone and plastic injection molding, liquid silicone injection molding, compression molding, extrusion molding, 3D printing, CNC machining, metal stamping, post-processing, and parts assembly. This diverse capability allows us to deliver custom silicone solutions with precision and excellence.
Product Launch Services
Got an idea? Let us turn it into reality.
If you have a concept, we are here to help you bring it to fruition. With our extensive experience in product development, we thrive on partnering with you throughout the entire creation process. From guiding you through mold sourcing and design to delivering the final product to your customers, we are committed to supporting you at every stage. Let us leverage our expertise to ensure your idea becomes a successful reality.
One-stop Services
1. NDA Execution
Before we begin, our company will execute Non-Disclosure Agreement (NDA) documents to protect your intellectual property. Our engineers will engage in comprehensive discussions with your team to gather all relevant details about your project. Once we have a clear understanding of your requirements, we will create a customized form to document every aspect meticulously and then collaborate closely to provide you with an expedited solution plan for your silicone products.
2. 3D Drawing Confirmation
To expedite the development of your custom silicone products, please provide us with your product drawings (2D/3D) or physical samples. If you have 3D files in formats such as STEP/STP, IGES/IGS, or X_T, these are ideal. Our engineers will collaborate with you during the initial customization phase to refine your product design. After finalizing the details, we will generate a design draft and send you the completed 3D CAD drawing for review, including dimensions, multiple views, and overall appearance renderings.
3. DFM Confirmation
Design for Manufacture (DFM) is crucial to ensuring practicality, safety, and user satisfaction. Through DFM, potential production challenges or limitations can be identified, and recommendations for modifying and optimizing product designs can be provided. The DFM report will serve as the foundation for confirming all mold and product details during production, particularly for silicone products.
- Tooling: Details on mold size, cavity count, tooling lifespan, processing methods, and more.
- Product: Specifications on material, color, hardness, surface finish, and other essential details.
- Branding: Various printing methods available for logo application.
4. Prototyping
Before production, we offer the option of 3D printing prototypes or creating prototype molds for your silicone products. Utilizing computer-aided design (CAD) models, 3D printed prototypes are ideal for confirming both structural integrity and visual appearance. Prototype molds, typically used to test new designs before mass production, feature simplified and optimized structures that expedite the manufacturing process and reduce costs. Prototyping allows designers to test, evaluate, and improve product designs, ensuring that the final silicone products meet all requirements.
5. Trial Tooling
We begin by creating trial tooling, usually with a single cavity or fewer. This tooling is used to produce initial samples of the silicone product. Based on testing and evaluation, we make necessary adjustments to the sample tooling until the product meets all specifications. It is not advisable to proceed directly to mass production tooling, as any required modifications can lead to significant economic losses. The trial tooling is intended to confirm the prototype structure, not for mass production.
6. Mass Tooling
Once the sample is approved, we proceed with creating molds for mass production, which typically feature multiple cavities. Prior to mass production, we produce final samples using the production molds to ensure they meet your exact specifications.
- Cavities: The number of cavities in a mold determines how many identical silicone products can be produced in a single production cycle. While more cavities increase mold manufacturing costs, they decrease the per-unit production cost.
7. Molding Production
During the production of your silicone products, we will keep you informed at every stage to ensure timely delivery. We implement rigorous quality control measures throughout mass production to guarantee high-quality products. Our molding process specializes in high-precision, high-requirement parts manufacturing, including medical-grade silicone products. With advanced management, a first-class technical team, and world-class equipment (Arburg, 2KM, Multitech) operating in a dust-free workshop, we deliver superior products and services.
8. QC Inspection & Packaging
After mass production, all silicone products undergo trimming and additional quality control processes in our dust-free workshop. We conduct a 100% quality control inspection before packaging to ensure that every product meets the highest standards and client requirements. With years of experience, we have established strong relationships with packaging material suppliers. We can assist you in selecting customized packaging solutions that meet your specific needs and budget, including color boxes, hanger tags, and PET boxes.
9. Warehouse and Logistics
We maintain a dedicated warehouse for storing silicone products before shipment. Additionally, we offer logistics support upon request. Depending on the selected shipping method, delivery typically takes between one week and one month.
10. After-Sales Service
We are committed to delivering superior quality silicone products that fully meet your expectations. If you encounter any issues, please contact our sales or customer service team within 24 hours, and we will promptly address your concerns.