Custom Silicone Products Manufacturer & Supplier
- Our factory spans over 6,000 square meters, capable of handling large order quantities.
- With over 200 professionals, we offer comprehensive services in mold making, design, and silicone product functionality.
- We operate a dust-free workshop at a 10,000 level, ensuring the highest quality production environment.
About Milosilicone
Milosilicone's advanced liquid silicone injection molding capabilities enable us to produce high-quality LSR parts for silicone kitchenware, baby care products, medical devices, and bathroom accessories. We offer an infinite variety of configurations, sizes, colors, and part geometries. For detailed discussions about your upcoming project, please contact our office to speak with us directly.
Liquid Silicone Rubber (LSR) is a versatile and cost-effective material for a wide range of silicone molded parts. Odorless, tasteless, and hypoallergenic, LSR is the ideal choice for devices used in sterile environments. It boasts excellent fatigue and tear resistance, low compression set, high elongation, and superior thermal stability. These properties make LSR suitable for applications requiring exceptional durability, and it is available in medical, food-grade, and high thermal conductivity formulations.
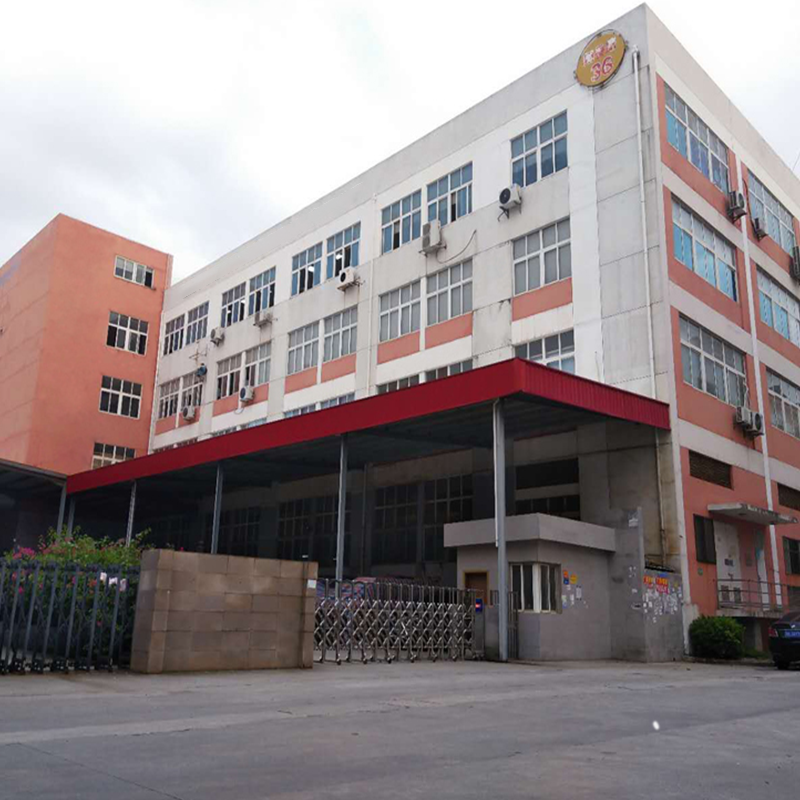
● Quality Assurance
Our factory is certified with ISO 9001:2015 and IATF 16949, reflecting our dedication to the highest manufacturing standards. Our silicone products have passed stringent tests and hold FDA, ROHS, LFGB, FAMA, and CPC certifications, ensuring safety, reliability, and superior quality.
● OEM Focus
As a custom silicone product manufacturer, we provide a comprehensive service model tailored to the unique challenges faced by entrepreneurs. Whether your silicone product is new, patent-pending, or in the prototype phase, we have the expertise to support you.
● One-Stop Service
We offer high-quality customized silicone products with options for personalized logos, diverse color choices, professional packaging, and molding services, all at competitive prices.
Our Custom Silicone Products Capability
Our professional engineering team has extensive experience serving a variety of industries. We offer rapid plastic injection molding, silicone injection molding, and silicone compression molding services to meet specialized silicone requirements efficiently.
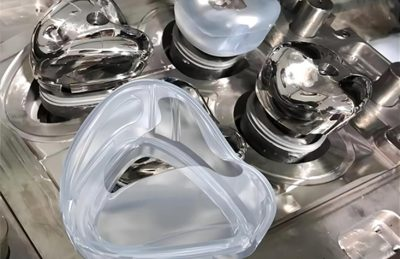
Liquid Silicone Rubber Molding
LSR molding is ideal for producing micro-sized, complex, and high-precision silicone components. Our fully automated production takes place in an ISO Class 8 clean room, ensuring the highest standards of quality and cleanliness.
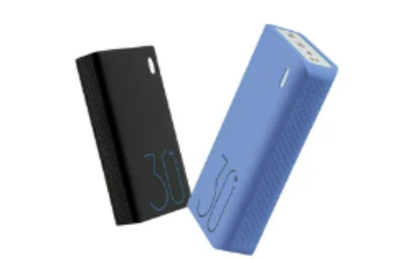
Silicone Compression Molding
Compression molding is a cost-effective and straightforward process. It allows the integration of silicone with various materials such as plastic, metal, and fabric into a single component, addressing a wide range of processing requirements.
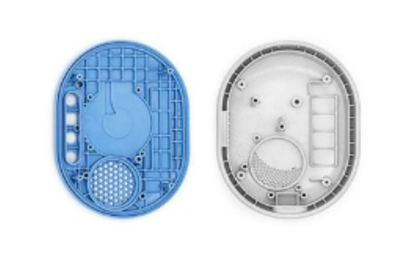
Plastic Injection Molding
Injection molding is capable of processing a wide array of resin materials. This method allows for the automation and mass production of parts with intricate shapes and high precision.
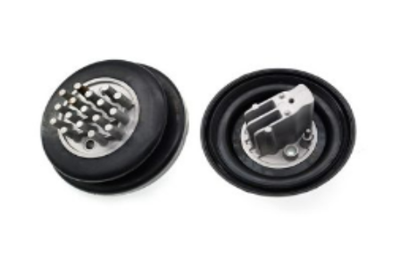
Overmolding & Insert Molding
These molding processes can seamlessly integrate multiple materials, such as silicone, plastic, metal, and carbon fiber, into a single component. This approach leverages the unique properties of each material to create superior, multifunctional parts.
One-Stop Services For Silicone Parts
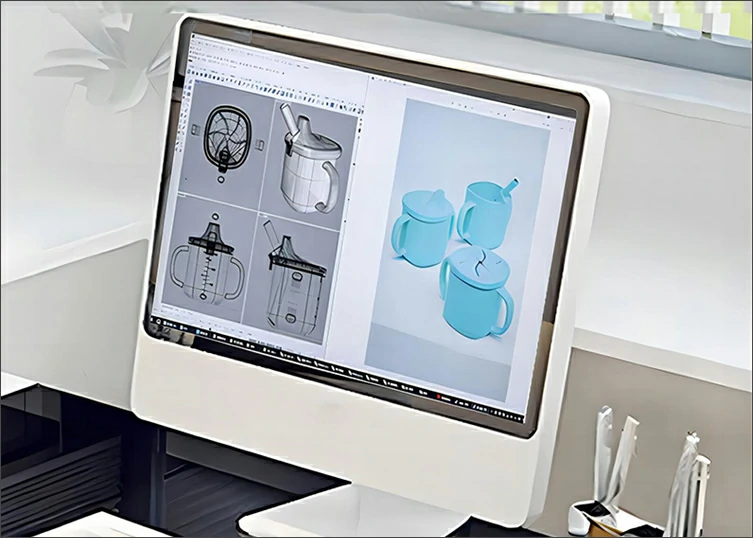
Product Design
Share your ideas with us, and we will combine them with our expertise to design your products. If you provide us with product samples, we can create enhanced and expedited prototypes for you.
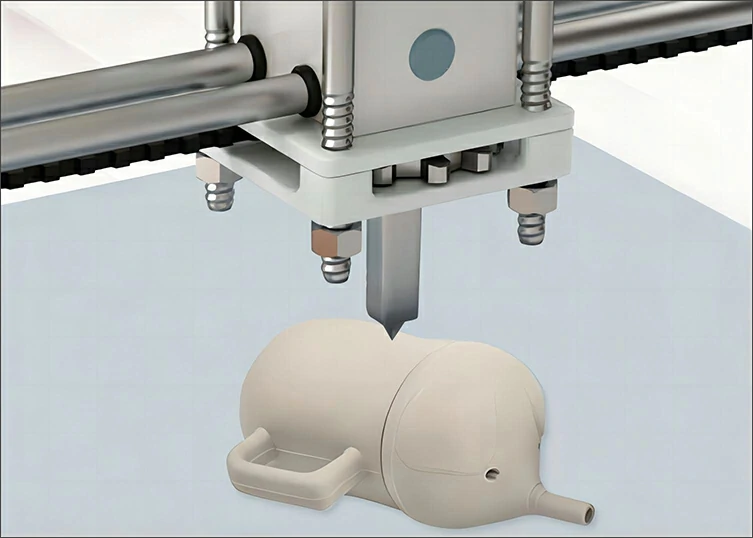
3D Prototype Making
Our advanced 3D printers can rapidly produce high-resolution prototypes, allowing you to physically assess and test your samples to ensure they meet your requirements. We make necessary modifications to the product design based on your feedback.
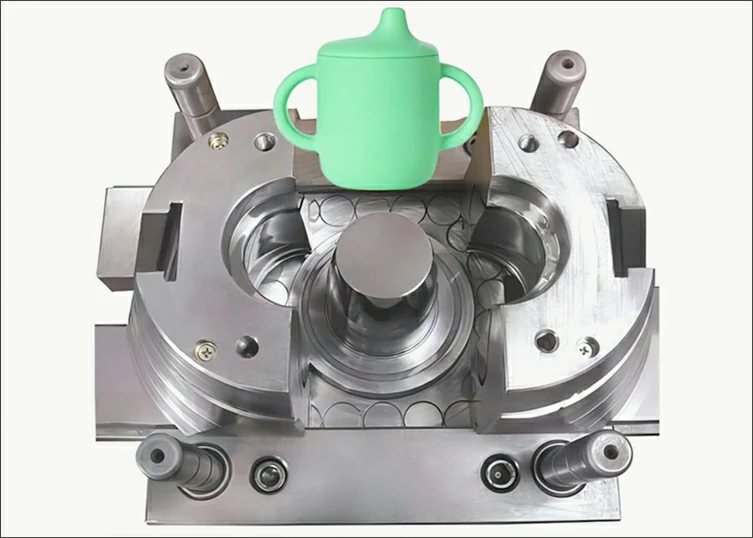
Tooling Creation
Our engineers perform Design for Manufacturability (DFM) analysis and design molds tailored to your specific product requirements. Once the mold is completed, it facilitates the efficient and cost-effective production of large quantities of identical parts.
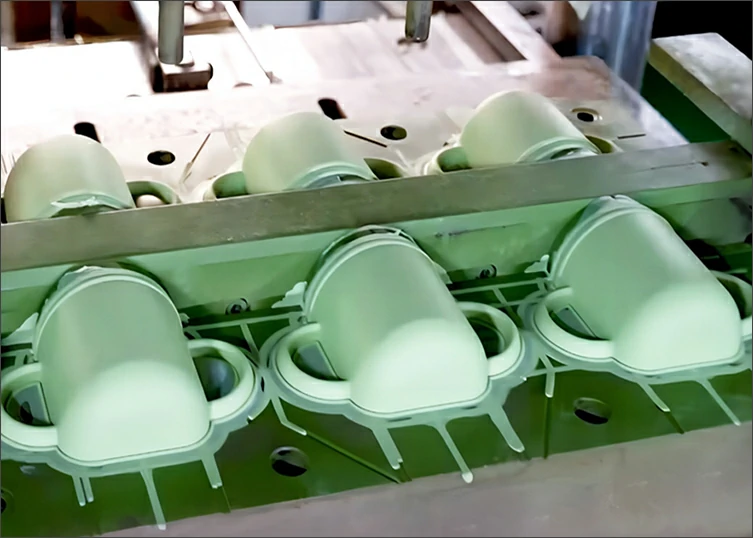
Mass Production
We will advise on appropriate processing methods for your needs. Inspection, packaging, and delivery occur after the completion of bulk production. This meticulously designed process ensures the production of high-quality products.
How To Collaborate with Us
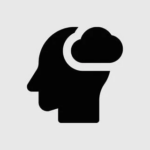
Non-Disclosure Agreement (NDA)
Building successful partnerships requires trust. We prioritize confidentiality, safeguarding your data and project details. Upon signing the NDA, we will engage deeply with your project and business objectives to ensure a thorough understanding.
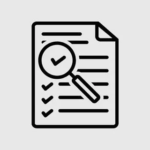
Request for Quote (RFQ)
The RFQ process showcases our competitive advantages and collective capabilities. It allows us to meticulously evaluate your information to create a comprehensive proposal. We accept file formats such as ProE (prt), IGES (igs), STEP (stp), and Parasolid (x_t). You can also send us samples for detailed evaluation.
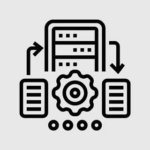
DFM Analysis
Our engineers will conduct a Design for Manufacturability (DFM) analysis on your products. This analysis helps us develop a practical process plan and provide precise pricing, ensuring an efficient manufacturing approach.
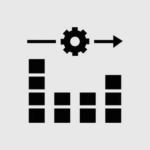
Manufacturing Agreement (MA)
The Manufacturing Agreement clearly defines and documents the legal, commercial, and service-level expectations for both parties. By addressing these elements upfront, we eliminate ambiguity and facilitate timely achievement of project milestones and commercial success.
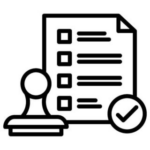
Sample Approval
Before full-scale production, we create samples of your product for approval. This stage allows you to assess quality and specifications to ensure they meet your requirements. Any necessary adjustments can be made at this point to align the final product with your expectations.
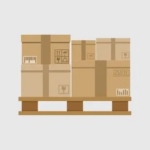
Production
Once samples are approved, we transition to full-scale production. Our advanced manufacturing processes and rigorous quality control measures ensure each product meets the highest standards. Throughout this phase, we maintain open communication, providing updates on progress and promptly addressing any concerns.